Introduction
The complex networks that link the different parts of electronic devices are called wire harnesses and they are frequently disregarded despite their importance. Because they transmit power data and electrical signals they are necessary for the efficient operation of everything from laptops and smartphones to cars and industrial machinery. Without these meticulously crafted bundles of wires our modern world would come to a complete halt.
1. Material Selection
The performance of electrical systems is greatly impacted by the selection of conductors and insulation materials. In order to reduce energy loss conductors—which carry electrical current—should have low electrical resistance. Because they are highly conductive copper and aluminum are frequently used. Nevertheless the ultimate choice is influenced by elements like price weight and corrosion resistance. Electrical current is kept from flowing where it should not by insulation materials.
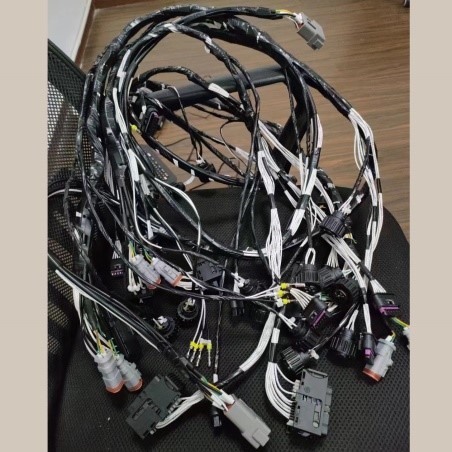
To endure the applied voltage without failing they need to have a high dielectric strength. Paper plastic and rubber are typical insulating materials. Cost chemical resistance and temperature resistance are some of the variables that influence the decision. For instance specific insulating materials like mica or silicone may be needed for high-temperature applications.
2. Design Precision
Wire harness design necessitates careful consideration of both mechanical and electrical properties. Electrically speaking elements like signal integrity, voltage ratings, and current carrying capacity are crucial. Connectors’ insulation type and wire gauge must all be carefully chosen to guarantee dependable and effective power and data transfer. The harness’s mechanical strength must be sufficient to endure the demands of its intended use.
For the harness to last a long time factors like vibration temperature fluctuations and exposure to chemicals or moisture must be taken into account. To reduce downtime and expenses the harness should also be made to be simple to assemble install and maintain.
3. Machining Technologies
Wire harness machining involves cutting, stripping, and crimping wires to create electrical assemblies. Several technologies are used for these tasks:
Wire Cutting:
- Laser Cutting: Precise cuts for various wire types and sizes.
- Die Cutting: Cost-effective for high-volume production of simple cuts.
- Mechanical Cutting: Suitable for field repairs and small-scale production.
Wire Stripping:
- Mechanical Stripping: Uses blades or rollers to remove insulation.
- Thermal Stripping: Uses heat to melt and remove insulation.
- Chemical Stripping: Uses chemicals to dissolve insulation.
Wire Crimping:
- Manual Crimping: Suitable for small-scale production and field repairs.
- Semi-automated Crimping: Increases productivity and reliability.
- Fully automatic crimping process: Produces accurate crimps at high speeds and volumes.
The type of wire production volume necessary precision and cost all influence the technology selection. For instance manual crimping may be adequate for small-scale or prototype work but fully automated crimping is best suited for producing intricate harnesses on a large scale.
4. Soldering Quality Control
Since soldering directly affects the devices dependability and functionality it is an essential step in the wire harness assembly process. Using the appropriate tools and materials and adhering to established protocols are essential for ensuring proper soldering
- Make sure the wire ends and connector terminals are free of contaminants that could interfere with the soldering process.
- To guarantee that solder melts uniformly and slides into the joint smoothly use a soldering iron that is set at the proper temperature.
- Apply enough solder to ensure a sturdy and long-lasting connection.
- To avoid cold joints or bridging do not use too much solder.
- Examine the joints for any flaws such as significant solder cracks or voids after soldering.
- Use a magnifying glass or microscope to ensure that the connection is perfect and tight.
5. Insulation and Protection
In electrical systems insulation layers are necessary to stop current from flowing in inappropriate places. Environmental factors operating temperature and voltage level all influence the choice of insulation material. Higher voltages or harsher environments might call for several layers of insulation.
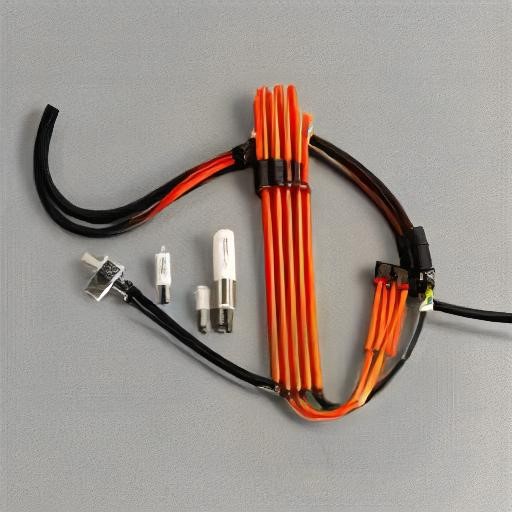
To guarantee the security of electrical equipment and personnel protective measures are essential. These precautions include enclosures shielding and grounding. A low-resistance path for electrical current to safely travel to the earth is provided by grounding. Shielding protects delicate parts and lessens electromagnetic interference. Physical defense against risks like dust moisture and mechanical impact is offered by enclosures.
To guarantee the security and dependability of electrical systems careful consideration must be given to the choice of protective materials and insulating layers.
6. Testing and Verification
To find possible flaws in wire harnesses before they are put into electronic devices a thorough testing procedure is necessary. Manufacturers can make sure their products fulfill the necessary requirements for quality dependability and safety by putting harnesses through a rigorous testing process. This is just one of the many testing techniques that can be used.
- Visual Inspection: Any evident flaws like loose cables broken connectors or improper routing can be found with a closely examined visual examination.
- Electrical Testing: To make sure the harness satisfies the requirements electrical tests measure its resistance capacitance and other electrical characteristics.
- Environmental Testing: To evaluate a harness’s performance under different circumstances it may be put through environmental tests like vibration humidity and temperature cycling.
To ensure that the harness operates as intended functional testing replicates the devices real-world operating conditions. The risk of product failures and recalls is decreased when manufacturers carry out a comprehensive testing procedure to find and fix any problems before the harnesses are shipped to customers.
7. Environmental Factors Consideration
Environmental factors have a major impact on wire harness performance and design. The materials used in wire harnesses can deteriorate when exposed to harsh environments such as high humidity extremely high temperatures chemicals and vibration. These elements need to be carefully taken into account by wire harness designers in order to guarantee dependable operation in demanding environments.
Choose materials that won’t be affected by changes in temperature. Make use of materials resistant to corrosion and moisture. Select materials resistant to degradation in the presence of common solvents or chemicals. The least amount of stress should be incorporated into the harness design to avoid wire breakage.
8. Cost-Benefit Analysis
One of the most difficult problems in wire harness manufacturing is keeping costs under control without sacrificing quality. The following are some important factors to think about.
Material Selection: Cost and quality can be greatly impacted by the selection of appropriate materials. It may seem appealing to use less expensive materials but it’s crucial to make sure they fulfill the necessary performance requirements and don’t shorten the harness lifespan.
Production Procedures: Improving production procedures can lower expenses without compromising quality. Increasing production efficiency automating processes or applying lean manufacturing concepts could all be part of this.
Design optimization: Costs can be reduced by using less material and streamlining the manufacturing process with careful design considerations. Without compromising performance manufacturers can cut costs by simplifying the harness design and getting rid of extraneous parts.
Quality Control: Defects and rework which can be expensive can be avoided by investing in strong quality control procedures. Effective testing and inspection methods can help manufacturers make sure their goods fulfill regulations and prevent expensive recalls.
Manufacturers can successfully manage expenses while upholding high standards of quality in the production of wire harnesses by carefully weighing these variables and putting the right plans into place.

9. Continuous Improvement
In the current competitive environment companies need to continuously work to enhance their procedures and outputs. This can be accomplished in part by adopting cutting-edge technologies. Production processes can be completely transformed by automation AI and data analytics which will boost productivity lower costs and improve quality. Businesses that invest in cutting-edge technologies can:
- Simplify operations: Automate monotonous jobs to cut down on human error and boost output.
- Improve decision-making: Make wise decisions by utilizing data analytics to obtain insightful knowledge.
- Boost the quality of your products: Use AI-powered quality control methods to guarantee uniform standards.
10. Conclusion
At every step of the process careful attention to detail is necessary to produce wire harnesses of the highest caliber. Each stage is crucial to guaranteeing the dependability and functionality of these crucial parts from design and manufacturing to testing and quality control. Manufacturers can streamline their wire harness production processes cut expenses and produce goods that satisfy the strictest quality and safety requirements by following best practices and putting effective strategies into place.
External links:
https://en.wikipedia.org/wiki/Cable_harness
https://www.wireterminalstrength.com/pull-test-standards-and-methods
https://www.linkedin.com/pulse/printing-wiring-harness-disrupting-industry-two-steve-bennington
https://fractory.com/soldering-explained/
https://en.wikibooks.org/wiki/Practical_Electronics/Soldering