Introduction to Sheet Metal Processing
Sheet metal, which is thin and flat, is a versatile material utilized in infinite industries. From automobile components to household home equipment, sheet metal processing shapes the sector around us. Information on the numerous strategies involved in manipulating sheet metal is vital for engineers, designers, and producers. By learning these methods, we can create innovations that meet the needs of present day society.

Sheet Metal Processing Methods
Sheet metal processing involves shaping and forming flat metal sheets into three-dimensional components. Two primary methods are sheet metal fabrication and stamping.
Sheet steel fabrication gives high flexibility, making an allowance for complex shapes and one-off designs. It is best for low- extent production and prototyping. However, it may be labor- intensive and much less efficient for high- extent production. Fabrication presents design flexibility, shorter lead times for low- extent production, and decrease initial setup expenses. However, it is much less efficient for high- extent production and labor- intensive methods.
Stamping, then again, makes use of specialized dies and presses to unexpectedly shape identical components. It is fantastically efficient for high- extent production and may produce intricate shapes. However, it requires considerable prematurely investment in tooling and is much less suitable for low- extent or custom designed components. Stamping gives high- velocity, high- extent production, particular and regular components, and decrease in line with-unit fee for high volumes. However, it has high initial tooling expenses, much less flexibility for design changes, and is restrained to repetitive shapes.
Handcrafted Precision: Sheet Metal Fabrication
Sheet metal fabrication is an meticulous manner that includes reworking flat metal sheets into intricate 3-dimensional components. It is an testimony to the artistry and precision of skilled craftsmen and advanced equipment. The adventure starts with particular slicing, regularly done via modern-day laser slicing or water jet slicing technologies. These strategies allow for intricate designs and complicated shapes to be excised from the sheet metal with remarkable accuracy.
Once the desired shapes are reduce, the manner of hole-making commences, commonly using drill presses to create particular openings for numerous functions. The subsequent step includes bending and forming the metal into the desired configuration. This could be performed via manual bending strategies, in which skilled artisans appoint hand equipment to form the metal, or via the usage of specialized equipment like press brakes.
These machines exert colossal force to bend the metal to precise angles and curves. One of the giant blessings of sheet metal fabrication is its flexibility in coping with complicated shapes. Whether or not it is an easy enclosure or an tremendously intricate component, skilled fabricators can deliver designs to existence. This adaptability makes sheet metal fabrication an precious manner for industries starting from automobile and aerospace to electronics and creation.
High-Volume Efficiency: Stamping Processes
Stamping is a excessive- volume manufacturing technique that involves shaping metallic sheets into preferred forms the usage of specialized dies and presses. It’s far specially green for producing huge quantities of equal elements, making it a cornerstone of industries like car, appliance, and electronics.
Huge-scale stamping device, along with hydraulic presses and mechanical presses, is employed to exert tremendous pressure at the metallic sheet, forcing it to conform to the elaborate shapes of the die. This technique is pretty automated, allowing for non-stop die processing and fast manufacturing costs. but, the excessive preliminary funding in tooling and the complexity of die design and protection can be significant demanding situations.
Even as stamping gives fantastic efficiency for excessive- volume manufacturing, it’s far much less bendy in relation to design modifications. Enhancing present dies or designing new ones can be time- eating and pricey. additionally, the tooling itself is at risk of put on and tear, requiring ordinary protection and substitute.
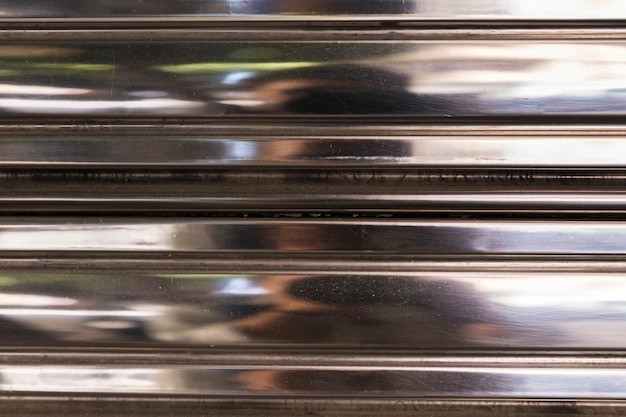
Artisan Skills in Hand Operations
Hand operations in sheet metallic fabrication require a blend of skill, precision, and safety cognizance. When drilling close to edges, it’s crucial to apply warning to save you the drill bit from breaking thru and probably injuring the operator. Using a backer board in the back of the workpiece can help to aid the fabric, decreasing the danger of breakage and ensuring a easy, specific hollow.
Skilled fabricators own a deep information of hand equipment, along with hammers, chisels, and documents. These equipment are invaluable for elaborate work that won’t be feasible with machinery. Via studying these strategies, craftsmen can create particular and customized additives with fantastic attention to detail. even as hand operations can be slower than machine- primarily based approaches, they provide remarkable flexibility and precision, making them critical for certain applications.
Design Considerations for Sheet Metal
Effective sheet metal design requires careful consideration of various factors to ensure manufacturability and optimal performance. One crucial aspect is flat pattern development, which involves converting a 3D part into a 2D layout that can be efficiently fabricated. This process demands a deep understanding of material properties, bending techniques, and springback effects.
Another critical consideration is the sequence of bends. The order in which bends are performed significantly impacts the final shape and accuracy of the part. Careful planning is essential to minimize distortion and ensure precise dimensions.
Furthermore, integrating fabrication knowledge into the design phase is vital. By considering factors like material thickness, bend radii, and tooling limitations, designers can create parts that are not only aesthetically pleasing but also practical to manufacture. By collaborating closely with fabricators, engineers can optimize designs for efficiency and cost-effectiveness.
Future Trends in Sheet Metal Technology
The destiny of sheet metal generation is poised for considerable improvements. modern equipment, inclusive of advanced laser reducing and bending systems, will hold to push the bounds of precision and performance. The mixing of clever manufacturing practices, such as automation, robotics, and synthetic intelligence, will revolutionize production strategies, permitting more flexibility and responsiveness.
As generation evolves, the call for for custom and excessive- extent production will force innovation. producers could be capable of tailor merchandise to unique needs, even as concurrently scaling up production to satisfy marketplace demands. The seamless integration of layout, engineering, and manufacturing strategies will streamline operations and reduce lead times.
Conclusion: Embracing Sheet Metal Expertise
Sheet metal processing, a harmonious blend of artistry and engineering, has been explored for the duration of this discussion. From the precision of laser reducing to the electricity of stamped components, we’ve delved into the numerous techniques that form our global. Through studying those competencies and embracing the modern day technologies, designers and producers can liberate the full ability of sheet metal. Permits hold to innovate, optimize, and raise the destiny of sheet metal processing.
Reference
https://en.wikipedia.org/wiki/Sheet_metal
https://en.wikipedia.org/wiki/Stamping_(metalworking)
https://cdn.thomasnet.com/kc/104/doc/ESI-Metal-Stamping-Design-Guide-v7.pdf
https://www.quora.com/What-is-sheet-metal
https://www.designingbuildings.co.uk/wiki/Metal_fabrication
https://web.mit.edu/2.810/www/files/lectures/2015_lectures/lec6-sheet-metal-forming-2015.pdf