Introduction
The interwoven web of wires and connectors known as cable assemblies is essential to modern industry. These assemblies are crucial to enabling the smooth flow of power and information in everything, from the complex circuits of electronic devices to the enormous infrastructure of telecommunications networks. For innumerable products and systems to operate and function at their best, their accuracy and reliability are necessary.
Precise Dimensional Control
For cable assemblies to function correctly and be compatible with other parts, their exact measurements are essential. Abnormalities in the given dimensions can result in a variety of issues such as mechanical failures, electrical interference, and decreased system efficiency.
Mold wear is one of the main reasons for inaccurate dimensions. Repeated use over time may result in molds that are damaged or deformed which will affect the assembly dimensions.
An additional element that may lead to dimensional errors is material shrinkage. Materials may slightly shrink as they cool and solidify which could have an impact on the assembly’s final measurements. Manufacturers should make an investment in high-precision molds that are made to hold their accuracy over time in order to overcome these difficulties.
For molding equipment to provide consistent dimensional control, regular calibration and maintenance are also necessary. The quality and dependability of cable assemblies made by manufacturers can be greatly increased by putting these tactics into practice.
Material Compatibility Strategy
In order to guarantee cable assemblies long-term performance and dependability, material selection is essential. Different materials not working well together can cause a number of issues including corrosion early aging and electrical failures. For instance, if exposed to specific chemicals or environmental factors, PVC a material that is frequently used in cable assemblies may age prematurely.
Before choosing materials for their assemblies, manufacturers should carry out extensive material compatibility testing to prevent these problems. This entails determining how well-suited various materials are to varied environments such as those with varying temperatures, humidity levels, and chemical exposure. The robustness and dependability of cable assemblies can be considerably increased by manufacturers by carefully evaluating material compatibility.
Welding Process Optimization
While welding is an essential step in the production of cable assemblies, using subpar welding techniques can result in a number of issues. For instance, assemblies may fail under stress due to weak weld points which could result in mechanical or electrical malfunctions. Manufacturers should optimize the welding parameters (welding current voltage and travel speed) to address these problems.
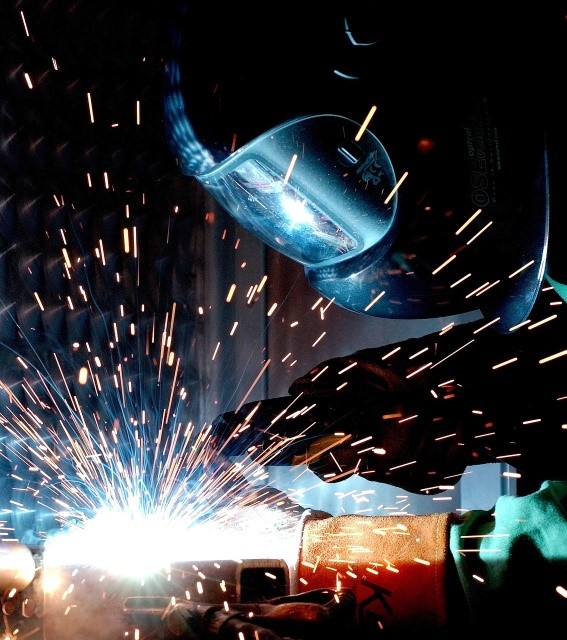
Furthermore, employing automated welding equipment can support maintaining accuracy and consistency in the welding process. Manufacturers are able to greatly enhance the dependability and quality of their cable assemblies by putting these strategies into practice.
Improved Overmolding Application
Overmolding is a crucial step in creating cable assemblies that involves merging multiple materials into one component. There are several advantages associated with this approach, including increased longevity, improved performance, and enhanced appearance. But it can also face different difficulties that could affect the end products quality.
Common Overmolding Issues
- Air Bubbles: If trapped within the overmolded assembly can reduce its strength by creating empty spaces, potentially compromising its structural integrity.
- Unequal Material Allocation: Variances in thickness appearance and function can occur due to an uneven distribution of materials.
- Delamination and premature failure: These may result from incomplete bonding which is the insufficient adherence between the overmolded material and the base material.
Approaches for Enhancement
Manufacturers should put these strategies into practice to ensure that high-quality overmolded assemblies are produced while addressing these challenges.
Precise Regulation of Injection Molding Specifications:
- Temperature: To guarantee ideal flow and curing, carefully check and modify the temperature of the base material as well as the overmolding material.
- Pressure: To avoid air entrapment and guarantee correct material distribution, maintain the proper pressure throughout the injection process.
- Injection Speed: Regulate the injection speed to reduce air entrapment and prevent undue turbulence.
Optimized Mold Design:
- Vent Locations: Strategically place vents in the mold to allow trapped air to escape and prevent air bubbles.
- Gate Placement: Carefully consider the location and size of the gate to ensure even material flow and prevent air pockets.
- Mold Surface Finish: A smooth mold surface can help to prevent material sticking and improve the overall quality of the overmolded assembly.
Appropriate Mold Release Agents:
- Selection: To ensure easy ejection and avoid sticking, select mold release agents that are compatible with both the base material and the overmolded material.
- Application: Ensure that the mold release agent is applied uniformly and steadily to every surface of the mold.
With the use of these techniques, producers may raise the caliber and consistency of their overmolded cable assemblies to a great degree which will benefit their customer satisfaction performance and durability.
Enhanced Shielding Efficacy
As a vital step in the manufacturing of cable assemblies, shielding keeps delicate parts free from electromagnetic interference (EMI). A number of issues such as unstable systems, decreased performance, and data corruption can result from inadequate shielding. Manufacturers need to choose shielding materials carefully, making sure they are appropriate for the intended use in order to ensure effective shielding. Environmental influences, the necessary attenuation level, and the electromagnetic interferences frequency range must all be taken into account.
To attain optimal shielding performance, appropriate application techniques must also be used. In order to maintain a consistent path for electromagnetic interference, the shielding material should be properly grounded and applied without any gaps. Manufacturers can greatly enhance the safeguarding of their cable assemblies and protect sensitive components from electromagnetic interference by adhering to these recommendations.
Environmental and Performance Evaluation
A number of different systems and devices depend heavily on the durability and dependability of cable assemblies. Thorough testing is necessary to ensure that these assemblies can resist the difficulties presented by various environments and operating conditions. Testing cable assemblies for environmental adaptability entails exposing them to a variety of circumstances such as high humidity low temperatures vibration and chemical exposure. By testing the assemblies, it is possible to find possible weaknesses and make sure they can continue to function well in harsh environments.
To evaluate the overall functionality and reliability of cable assemblies, extensive performance evaluation is required in addition to environmental testing. This entails evaluating elements like mechanical strength, electrical resistance, and signal integrity. Manufacturers can learn a great deal about the capabilities of their cable assemblies and make well-informed decisions about their design materials and manufacturing processes by carrying out environmental and performance testing.

Conclusion
The producers of cable assemblies face a variety of intricate problems that call for innovative solutions and a commitment to continuous improvement. By handling dimensional control, material compatibility, welding techniques, overmolding, shielding, and environmental adaptability, manufacturers can significantly increase the quality, dependability, and performance of their products. This presentation outlines various concepts such as precision molding, material testing, optimum welding, enhanced overmolding techniques, proper shielding, and thorough environmental testing that provide guidance for creating top-notch cable assemblies. Acknowledging the continuous evolution of the field and the emergence of new opportunities and challenges is essential. Manufacturers must continuously seek new technologies and best practices to stay competitive in the cable assembly market.
External links:
https://en.wikipedia.org/wiki/Cable_harness
https://web.archive.org/web/20190407004354/https://www.wirafe.com/how-is-a-cable-harness-designed/
https://www.wireterminalstrength.com/pull-test-standards-and-methods
https://en.wikipedia.org/wiki/Injection_moulding#overmoulding