Introduction: The Challenge of Color Changeovers in Injection Molding
Injection molding is the heart of modern manufacturing, producing everyday household items to complex self-propelled components, One of the persistent operational challenge in this is color changeover in Injection Molding, the process of switching from one plastic color to another.
Though it sounds simple, changing colors requires thoroughly cleaning out the remains of previous material from the machine’s screw and barrel, This task is not only time-consuming but also wasteful, For manufacturers juggling multiple color variants, these carelessness can quickly erode profit.
As industries move toward sustainable and cost-effective solutions, strategies like spare screw barrel replacement are rising as game-changers.
Screw Barrel Functionality: The Role in Plastic Melting and Transport
It’s essential to understand the critical role of the screw barrel assembly to appreciate this solution, in injection molding machines.
The screw rotates inside the barrel, feeding plastic pellets from the hopper through various heating zones. As the material moves along the screw, it melts uniformly, is mixed thoroughly, and is eventually injected into the mold cavity at high pressure.
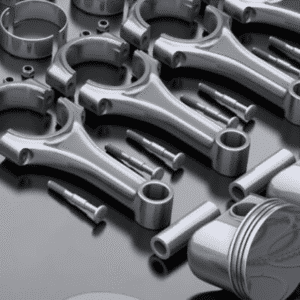
Key functions of the screw barrel include:
- Melting: Ensuring consistent thermal distribution for uniform plastic melt
- Mixing: Achieving homogeneity of material and colorants
- Transporting: Moving material from the hopper to the mold
- Metering: Controlling the quantity of plastic injected into the mold
Traditional Cleaning Methods: The Wasteful Process of Barrel Purging
When switching colors, traditional practice dictates that operators purge the screw barrel by running virgin resin, purging compounds, or cheap regrind material through the machine until all traces of the previous color are gone.
This process has several downsides:
- Material waste: Several kilograms of plastic can be consumed during purging, material that could otherwise be turned into saleable products
- Energy consumption: The machine consume unnecessary electricity while continuously operating at high temperatures
- Environmental impact: The wasted material often ends up in landfill
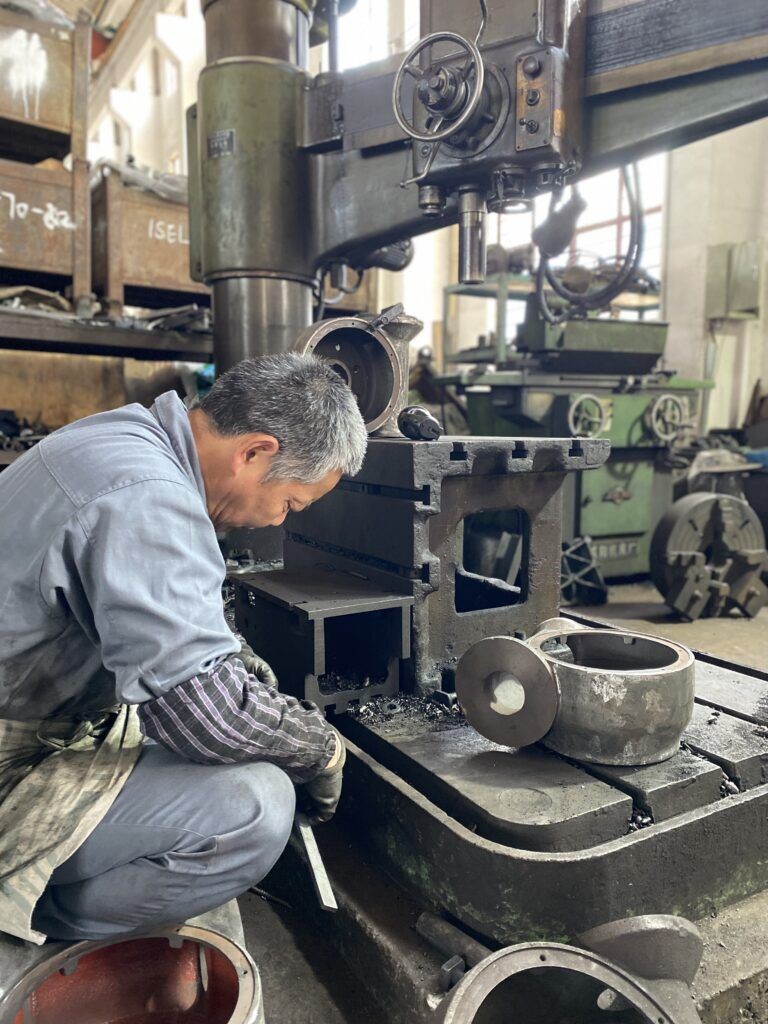
Innovative Solution: Implementing Spare Screw Barrels for Color Changes
Instead of laboriously cleaning the barrel in situ, manufacturers can:
- Remove the contaminated screw barrel assembly after a production run.
- Replace it immediately with a clean spare barrel, prepped with the new material and color.
- Clean the removed barrel offline, using controlled, efficient cleaning processes without tying up machine time.
This strategy offers multiple advantages:
- Barrel replacement is significantly faster than purging, reducing changeover times dramatically.
- Eliminates the need for extensive purging runs.
- Machines spend less time idling at high temperatures, cutting electricity usage.
- Cleaner, faster changeovers mean fewer defective parts during startup.
Cost Savings Analysis: Calculating Material and Energy Reductions
Let’s put this into perspective with some numbers.
Material savings
Assume a typical color change in a medium-sized injection molding machine requires purging 5-10 kg of resin or purging compound per changeover. If your facility performs 200 color changes per year:
- Traditional method: 5 kg × 200 = 1,000 kg of wasted material annually
- Spare barrel method: Near-zero waste on changeover
If your material costs $2/kg, this alone could save $2,000 annually per machine, not counting compound costs, which can be much higher.
Energy savings
Consider that purging can require an extra 30–60 minutes of machine operation at high energy levels. If a machine consumes 20 kWh during this period:
- Traditional method: 20 kWh × 200 = 4,000 kWh annually
- Spare barrel method: Reduced machine runtime = lower consumption
At $0.10 per kWh, that’s another $400 saved annually per machine, not to mention the extended lifespan of machine components due to less thermal cycling and wear.
Implementation Details: Selecting and Managing Spare Barrel Inventories
For manufacturers considering this approach, success hinges on careful planning and management of spare screw barrel inventories.
Key considerations:
- Compatibility: Spare barrels should match machine specifications exactly
- Storage: Barrels should be stored in a measured environment to stop corrosion
- Cleaning process: Offline cleaning can contain advanced tools like ultrasonic tanks
- Operator training: Staff must be trained to handle barrel replacement safely
- Tracking system: A barcode or RFID-based inventory system can help track barrel use,
However the early investment in spare barrels and handling equipment may seem important, the operational benefits and long-term savings defend the outlay.
Environmental Impact: Reducing Waste and Carbon Footprint
The spare barrel strategy directly contributes to sustainability goals:
Reduced plastic waste
Every kilogram of resin saved means less demand for virgin plastic production a major source of greenhouse gas emissions.
Lower energy usage
Energy savings from reduced purge times contribute to a smaller carbon footprint, providing valuable compliance support.
Enhanced recyclability
Since removed barrels can be cleaned thoroughly offline, any residual plastic can often be reclaimed and reprocessed, further improving resource efficiency.
Case Study: Successful Adoption in a Leading Injection Molding Facility
A European automotive supplier recently adopted spare screw barrel replacement across its injection molding operations.
The challenge
The plant produced interior trim components in over 20 colors. Frequent color changes led to high purge costs and machine downtime, impacting delivery schedules and margins.
The solution
The company invested in:
- Two spare barrel assemblies per major machine line.
- Custom barrel carts for safe transport.
- A dedicated offline cleaning station with automated equipment.
The results
- Material savings: 1.2 metric tons of resin saved in the first year
- Energy savings: 6,000 kWh reduction
- Changeover time: Cut from 45 minutes to 10 minutes
- ROI: The project paid for itself within 18 months
ROI Calculation: Justifying the Investment Through Long-Term Savings
How do you know if this strategy is right for your operation?
Sample ROI model:
- Initial investment: $25,000
- Annual material savings: $2,000 per machine × 5 machines = $10,000
- Annual energy savings: $400 per machine × 5 machines = $2,000
- Downtime reduction: Freed machine time = increased production = additional revenue
In this model, the investment breaks even in about two years, and delivers ongoing savings every year after that.
For high-volume or multi-color facilities, ROI could come even faster, especially when you factor in reduced defective parts, and lower maintenance costs.
Future Trends: Advancements in Screw Barrel Design and Efficiency
The spare screw barrel concept is just the beginning, Looking ahead, manufacturers can expect:
- Quick-change barrel couplings: Designs that allow minimal-tool barrel swaps
- Advanced coatings: Barrels with coatings that resist buildup, making them easier to clean
- Integrated sensors: Barrels with embedded temperature for smarter maintenance
- Automation: Robotic systems for barrel handling to reduce manual labor
These innovations will make adopting spare barrel strategies more beneficial.
Conclusion: Embracing Change for Sustainable Manufacturing Practices
Color changeovers have been a source of frustration and waste in injection molding. But with innovative approaches like spare screw barrel replacement, manufacturers can tackle this challenge head-on.
The result?
- Significant material and energy savings
- Reduced carbon footprint
- Improved production flexibility
- Faster ROI on capital investments
In a world that is focused on efficiency, accepting such solutions isn’t just smart, it’s essential for long-term competitiveness. The time to rethink your changeover strategy is now.
Refference:
https://art-tangent.com/capability
https://en.wikipedia.org/wiki/Nurdle_(bead)
https://en.wikipedia.org/wiki/Radio-frequency_identification