Introduction
Molding finishing is an essential step in the production process that significantly impacts a products’ appearance, durability, and functionality. By applying various treatments and procedures, manufacturers can enhance the molded parts’ efficiency and look. Surface marks, color irregularities, and dimensional errors in molded items can be caused by improper finishing. These flaws not only reduce the quality of the product but also weaken its functionality. For instance, a surface that is not finished well might be more prone to scratches, corrosion, or contamination, which can result in early signs of damage.

External Surface Acceptance
The acceptance of machine marks on external surfaces depends on several factors, including the product’s intended use, aesthetic requirements, and functional specifications. For products where appearance is paramount, strict tolerances may be applied to minimize the visibility of machine marks. However, in applications where functionality takes precedence, slight imperfections may be acceptable as long as they do not compromise the product’s performance.
To address machine marks and ensure acceptable surface finishes, selective deburring strategies can be employed. This involves selectively removing material from specific areas of the molded part to reduce the prominence of sharp edges or burrs. Techniques for deburring can involve both automated procedures like vibratory finishing or tumbling and manual procedures like trimming or filing. The parts geometry material and intended level of finish all influence the deburring technique selection.
Internal Surface Challenges
Because the internal surfaces are difficult to reach and there is a chance that contaminants will become trapped, finishing molded parts can be challenging. To prevent internal flaws and preserve the integrity of the product, machining marks such as burrs or chips must be removed thoroughly.
To address these issues, different finishing methods can be applied. Chemical etching is useful for surface polishing and surface improvement while ultrasonic cleaning is effective at removing impurities from complex internal shapes. In order to reach difficult-to-reach places, mechanical finishing techniques like brushing or honing may occasionally be necessary. It is essential to select finishing techniques that protect the parts structural integrity and do not introduce new flaws.
Surface Treatment Techniques
Several surface treatment methods are frequently employed to attain different finishes on molded components including passivation grinding and polishing. Every technique has benefits of its own and works well for certain situations.

Abrasive tools are used in the mechanical process of grinding to remove material from the surface. It is frequently applied to produce a textured or rough finish. Conversely, polishing is a more delicate procedure that uses less material removal to smooth and refine the surface. It’s frequently applied to get a glossy mirror-like finish. By creating a shielding oxide layer on the surface, the chemical process known as passivation improves an objects resistance to corrosion.
To keep metals like stainless steel from rusting and to preserve their aesthetic appeal, it is frequently applied. The required level of finish the parts material characteristics and the particular application requirements all influence the surface treatment technique selection. For instance, polishing might be favored for products that need a smooth and reflective finish while grinding might be appropriate for items that need a rough surface for more friction or grip. When corrosion resistance is a crucial component, passivation is frequently utilized.
Roughness Control
RA 3.2 is a common roughness standard used to specify the surface finish of machined or molded parts. It refers to the arithmetic average roughness, measured in micrometers (µm). Meeting this standard is crucial for ensuring the product’s functionality, durability, and appearance.
To achieve RA 3.2 roughness, careful process control is essential. Factors such as machining parameters (cutting speed, feed rate, depth of cut), tool condition, and material properties must be carefully considered. Regular monitoring and inspection of the surface finish using profilometry or surface roughness measurement instruments are necessary to ensure compliance with the standard.
In addition to process control, specific techniques can be employed to improve surface roughness. For example, honing or burnishing can be used to reduce surface roughness and improve its finish. Regular maintenance of equipment and tooling is also critical to prevent defects that can affect surface quality.
Tooling & Equipment Selection
Achieving the required surface finish and guaranteeing effective processing depend heavily on the choice of suitable tooling and equipment.
In terms of accuracy, consistency, and speed, advanced deburring and finishing tools like robotic arms, automated grinding machines, and laser systems are very advantageous. Automation can save labor costs and increase process efficiency which is especially advantageous for high-volume production. Intricate or complex parts that need expert operators for accurate finishing however might still require manual processing. The parts geometry production volume and required level of finish are some of the variables that determine whether to process the part automatically or manually.
It’s crucial to take into account aspects like cost upkeep needs and compatibility with other manufacturing processes when choosing tools and equipment. Manufacturers can attain higher-quality final products and increase overall productivity by investing in cutting-edge tools and technologies.
Quality Assurance
During the post-molding finishing process, quality assurance is essential. To find and fix any flaws or imperfections that could lower the products quality, thorough inspection procedures are required. The common methods for evaluating the overall quality of the completed parts are visual inspection, dimensional measurement, and functional testing.
Because internal processing marks are inaccessible, ensuring their invisibility is particularly difficult. Non-destructive testing (NDT) techniques, such as ultrasonic testing and X-ray inspection, can be used to identify internal flaws in a part without causing damage.
By carefully examining both the internal and external surfaces, manufacturers can ensure that their products meet the highest quality standards and are free from flaws that could impair their performance or durability.
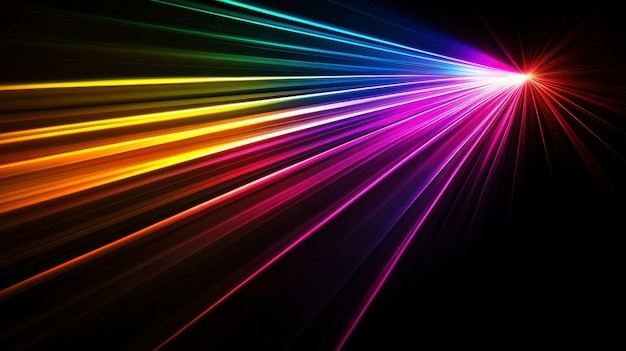
Copyright-free source: https://www.freepik.com/free-ai-image/spectrum-flashes-coloured-light_311089145.htm#fromView=search&page=1&position=34&uuid=a01ae58a-bb8a-419d-9be9-df7bb8438c7d
Conclusion
Using a variety of post-molding finishing techniques expertly can help manufacturers greatly increase the quality longevity and aesthetic appeal of their products. From careful surface preparation to advanced finishing methods and stringent quality control, a comprehensive strategy is required to get the best results. Achieving precision manufacturing requires constant improvement. Manufacturers can streamline their operations, lower error rates, and produce goods that surpass customer expectations by remaining abreast of emerging technologies and industry best practices.
External links:
https://en.wikipedia.org/wiki/Etching
https://www.engineersedge.com/manufacturing/surface-roughness-conversion.htm
https://books.google.com.ph/books?id=xdmNVSio8jUC&pg=PA349&redir_esc=y#v=onepage&q&f=false
https://en.wikipedia.org/wiki/Burr_(edge)
https://www.asnt.org/MajorSiteSections/About/Discover_Nondestructive_Testing.aspx
One Response
Thanks for sharing. I read many of your blog posts, cool, your blog is very good.