Introduction: The Evolution of IMD in Decorative Injection Molding
What started as a basic technique to add surface graphics later became a high-tech process that blends form and function, Across various industries like automotive, home appliances, and electronics, In-Mold Decoration (IMD) has changed the way plastic parts look and perform. It adds designs by blending decorative elements directly into the molding process, making parts durable and cost-effective. At the forefront, there are three key IMD methods:
- TYPE-TR
- TYPE-T
- TYPE-P
These techniques not only improve the aesthetics of the product, but also make the manufacturing process faster and more efficient.
TYPE-TR Transfer: Precision, Multi-color Decoration & Automotive Applications
The TYPE-TR (Transfer) method is an advanced In-Mold Decoration (IMD) method that, during the injection molding process, transfers only the printed design from a decorative film onto the plastic surface, Without any need to trim film margins, this technique allows high-precision and multi-color decorations making it ideal for applications that require intricate designs and seamless finishes.
TYPE-TR is mainly popular in the automotive sector, where interior and exterior parts require a combination of durability and visual appeal. Common applications are:
- Dashboard panels
- Center consoles
- Door trims
- Control buttons and switch panels
Particularly in high-demand industries like automotive and consumer electronics, TYPE-TR stands as a powerful solution for manufacturers aiming to combine visual excellence with streamlined production.
TYPE-S Simulforming: Merging Decoration with Forming for Complex Shapes
TYPE-S, or Simulforming is a technique that unites the decoration process with the plastic forming step, creating a seamless integration of decorative elements onto complex, three-dimensional surfaces. In this method, a thicker decorative film is preheated and then turned into the desired shape using vacuum or pressure forming before being placed into the mold for injection. TYPE-S Simulforming is great for products that require aesthetics along complex 3D shapes, commonly used in:
- Automotive interior components such as instrument panels, door panels, and trim parts
- Consumer electronics with curved displays or casings
- Home appliances featuring ergonomic, contoured surfaces
It’s a perfect fit of decorative film on complex shapes without forming any wrinkles, offering high durability suitable for frequent use even in harsh conditions. Moreover, it is a process with reduced waste and lower labor costs.
TYPE-P Pre-forming: Advanced Shaping Prior to Decoration for Custom Designs
TYPE-P, or Pre-forming is a technique that involves preheating and forming decorative film into the desired shape before the process of injection molding. This method allows correct placement of graphics on complex surfaces, making it ideal for custom and premium applications. TYPE-P is used in industries where visual details are very important:
- Automotive dashboards, gear knobs, and specialty trims
- Consumer electronics with tailored branding or unique casing designs
- Medical and industrial equipment with ergonomic, user-friendly interfaces
- Luxury appliance control panels and UI components
It empowers manufacturers to deliver custom, high-quality, and visually striking components, combining technical excellence with design creativity.
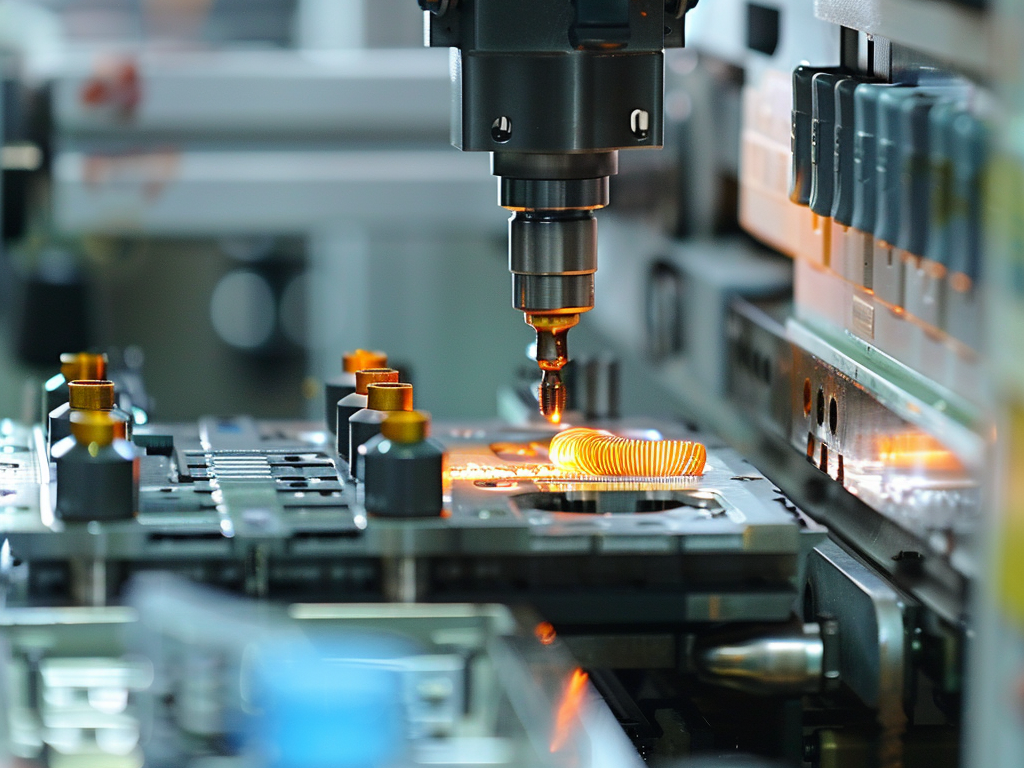
Process Mechanics: Understanding the Unique Characteristics of Each IMD Type
IMD Type | Decoration Method | Surface Complexity | Production Volume | Notable Features |
TYPE-TR | Ink transfer only (film-free) | Flat to mild curves | High | Fast, clean, precise multi-color prints |
TYPE-S | Formed film + injection | Complex 3D shapes | Medium to High | Integrated forming + high durability |
TYPE-P | Pre-shaped film + injection | Custom deep shapes | Low to Medium | Exact design placement, personalization |
Supply Chain Integration: Membrane Provision, Feeding Mechanisms, & Molds
- Membrane Provision:
The decorative film is the foundation of IMD, and its composition, print quality, and functional properties greatly influence the final product. High-quality decorative films are necessary for achieving desired aesthetics and durability. Suppliers should ensure consistent film quality and availability.
- Feeding Mechanisms:
Feeding systems are critical for positioning the film accurately within the mold, especially in high-speed production lines. Roll-to-Roll Feeders are for TYPE-TR, Robotic or Manual Film Loading for TYPE-P and TYPE-S. It reduces human error and material waste.
- Mold Design:
Molds used in IMD must be engineered to not only shape the final product but also accommodate and preserve the integrity of the decorative film during injection.
Workflow Analysis: Step-by-step Breakdown of the IMD Processes
TYPE-TR (Transfer Method) – Direct Ink Transfer for Clean Finishes
Ideal for: Automotive interiors, buttons, panels
- Film Feeding: A decorative film is continuously fed into the injection mold.
- Mold Clamping: Film aligns with the cavity; only the ink layer is transferred, not the film itself.
- Injection Molding: Molten plastic is injected behind the film.
- Ink Transfer: The printed design adheres to the plastic surface.
- Film Rewind: The used film rewinds, eliminating the need for trimming or waste handling.
TYPE-S (Simulforming) – Forming & Decorating in One Seamless Step
Ideal for: Complex 3D surfaces, dashboards, curved electronics
- Film Preheating: A thicker decorative film is heated to soften.
- Forming: Film is shaped using vacuum or pressure forming.
- Mold Placement: The shaped film is inserted into the injection mold.
- Injection Molding: Plastic is injected behind the film, creating a tight bond.
- Finished Part: The final product has wrinkle-free decoration over 3D surfaces.
TYPE-P (Pre-forming) – Precision Shaping Before Injection
Ideal for: Custom or premium products with unique surfaces
- Film Heating & Forming: Decorative film is preheated and formed into the desired shape in a separate step.
- Trimming: The formed film is trimmed to match the mold dimensions.
- Mold Insertion: The trimmed, shaped film is placed into the injection mold.
- Injection Molding: Plastic is injected to back the film and finalize the part.
- Result: Sharp alignment of design on complex surfaces with custom aesthetics.
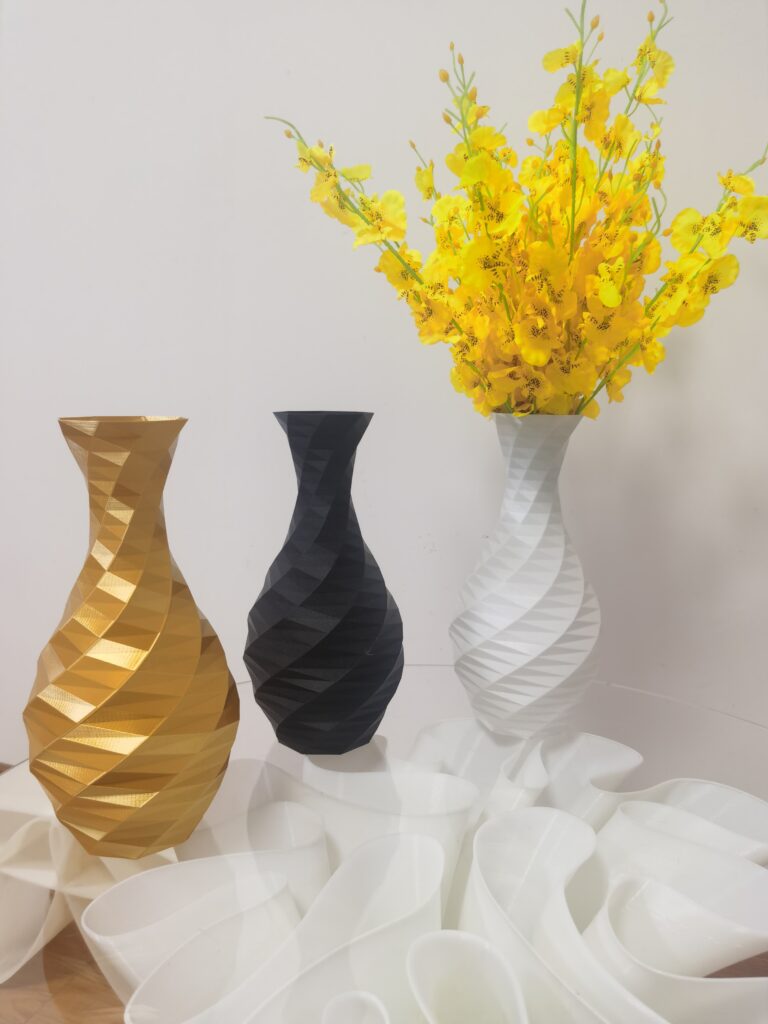
Case Studies: Real-world Applications in Automotive Interiors & Accessories
Automotive Interiors:
TYPE-TR has been used to produce textured leather-like surfaces on center consoles and armrests, giving a luxurious feel that elevates the overall interior quality without any extra coatings.
TYPE-S has been applied to create smooth, glossy finishes on instrument panels and trim pieces, delivering a sleek and modern look
Automotive Accessories:
TYPE-P is ideal for producing vibrant, durable designs on automotive accessories such as gear shift knobs and console panels.
Advantages & Limitations: Assessing the Benefits and Challenges of IMD
Advantages:
- Superior durability with decoration integrated into the molded part
- Vibrant, precise, and high-quality graphics
- Seamless, smooth surface finish without additional coating
- Reduces need for secondary painting or printing steps
- Saves time and lowers overall production costs
Limitations:
- Higher upfront tooling and mold design costs
- Complexity in mold manufacturing and process control
- Limited ability to apply extremely fine textures or details
- Requires strict material compatibility to prevent defects
- Less flexibility for last-minute design changes
Industry Impact: How IMD is Revolutionizing Decorative Plastics
IMD is revolutionizing the decorative plastics industry by enabling manufacturers to produce high-quality and visually appealing components in a single molding process, This reduces production time and costs. As a result, IMD is becoming the preferred method for many industries, driving new possibilities along elevating product aesthetics to meet consumer demands
Conclusion:
The advancements in IMD techniques, particularly TYPE-TR, TYPE-S, and TYPE-P, have opened new avenues for product design and manufacturing efficiency by integrating decoration into the molding process, manufacturers can achieve superior aesthetics, durability, and cost savings.
Reference:
https://www.art-tangent.com/product
https://art-tangent.com/capability/