The appearance and performance of metal components are significantly influenced by the quality of their surface finish. Two critical processes in achieving exceptional metal surfaces are mirror polishing and anodizing.
Are you aware that both play a crucial role in various industries’ operations?
For example, mirror polishing is used on engine components, interior trims, and external elements in the automotive industry. It is also used to give metals a glossy finish in jewelry and clothing.
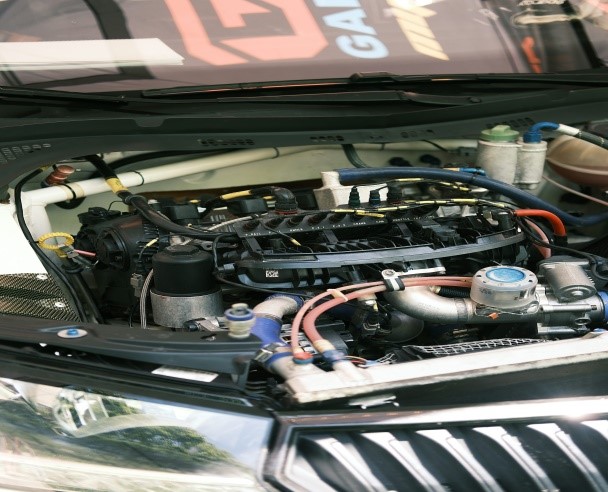
In contrast, anodizing is utilized in architecture and construction for outdoor cladding, window frames, and railings and fences. In electronics, it is also used to improve computer and mobile device performance.
Pre-Treatment Process
The pre-treatment stage involves two primary steps: cleaning and deburring.
- Cleaning – Contaminants are removed using detergents, ultrasonic cleaners, and other specialized cleaning tools.
- Deburring – This step deals with imperfections that may make polishing efficiently difficult. You can do sanding, filling, grinding, or tumbling. That way, you can eliminate sharp edges or burrs for better precision.
Mirror Polishing Techniques
Achieving a flawless mirror finish on a metal surface requires a multi-step process that demands precision.
Rough Grinding
The initial and most aggressive step, rough grinding, removes substantial amounts of material from the material’s surface. This stage targets significant imperfections, such as machining marks, casting flaws, or heat treatment scale. Coarse-grit abrasives, typically silicon carbide or aluminum oxide, are used to rapidly reduce the material and create a relatively flat surface, establishing a foundation for subsequent finer processes.

Fine Grinding
Following rough grinding, fine grinding refines the surface by removing scratches and imperfections left from the previous stage. Finer-grit abrasives gradually smooth the surface, preparing it for the polishing steps. Using the correct grit progression is essential to avoid creating new, deeper scratches. Cross-grinding, where the material is oriented differently between grinding stages, can help minimize scratch depth.
Polishing
Polishing introduces a high-luster finish to the workpiece. This stage involves using polishing compounds and wheels or buffs. The tiny scratches and imperfections are removed slowly by the abrasive particles in the polishing compounds, with the carrier aiding in distributing heat and lubricating the process. The choice of compound and wheel depends on the desired finish and the metal being polished.
Final Polishing
The last step of polishing is focused on attaining the perfect reflective shine. Superior polishing substances, frequently including diamond or cerium oxide abrasives, are utilized to eliminate final traces of scratches and imperfections.
Anodizing Process
Anodizing gives metal a firm and durable layer that protects it from rust and wear. It can also give the metal a nice look, with different colors and finishes possible.
Cleaning and Pre-Treatment
This stage aims to remove dirt and grease on the metal surface to get good results.
Here’s what each step does:
- Degreasing: To remove oily stuff from the metal.
- Alkaline Cleaning: To remove impurities stuck to the metal.
- Acid Etching: To create a surface for the new coating to stick to.
- Desmutting: To remove iron impurities on aluminum.
Anodizing Process
Key factors in anodizing:
- Electrolyte: This liquid, often an acid like sulfuric acid, helps create the oxide layer. Different liquids create different types of coatings.
- Current: The strength of the electric current controls how fast the oxide layer grows. Stronger current makes the layer thicker but can also make it rougher.
- Temperature: The liquid’s temperature affects how quickly the oxide forms and its properties. Cooler temperatures make a harder but thinner layer.
- Voltage: This controls how much oxygen is released during the process, which affects the oxide’s structure.
- Time: The longer the metal is in the bath, the thicker the oxide layer becomes.
Dyeing and Sealing
Dyeing is done to:
- Add color: You can put special colors to give the metal a new look. These colors can be from natural or artificial sources.
- Create a variety: This process allows you to make the metal almost any color you want, from bright and bold to soft and subtle.
On the other hand, sealing is done to:
- Protect the color: Once the color is in, we need to seal the holes to keep the color from fading or washing away.
- Improve durability: Sealing also makes the metal stronger and more resistant to scratches and corrosion.
Key Challenges and Solutions
Keeping the surface clean poses a major difficulty during mirror polishing and anodizing procedures. There are various approaches for removing oil and grease during their handling. However, how do you deal with tiny contaminants? In this case, you should look for a strong pre-treatment procedure specially designed for that task. Examples are ultrasonic cleaning and acid etching.
Then, there’s also the issue of precision. Achieving a flawless mirror finish demands exceptional precision and skill. Human error, equipment variability, and abrasive inconsistencies can all contribute to defects. Skilled operators with a deep understanding of polishing techniques are essential. Fortunately, you can use CNC polishing machines and other high-precision equipment for this purpose.

Finally, let’s talk about the different anodizing parameters involved. During the process, you have to have full control of the following variables: current, temperature, and electrolyte composition. Precise control of these variables is achieved through careful monitoring and adjustment. Regular electrolyte analysis, temperature control, and current regulation are essential.
Conclusion
Many manufacturers struggle with the significant challenge of producing metal surfaces that are both visually appealing and practical. To make it happen, there are two important processes — mirror polishing and anodizing. To achieve your desired outcomes, you have to demonstrate skill and make the most out of advanced machinery available. You also have to set strict quality control measures to prevent and overcome the common challenges that may arise at any time. Ensure that you complete these tasks in order to attain superior finishes that improve the aesthetic appeal and functional durability of your products.
External links:
1 https://en.wikipedia.org/wiki/Anodizing
2 https://www.instructables.com/Mirror-Finishing-A-Metal
3 https://www.sae.org/standards/content/ams2488d
4 https://www.anodizing.org/page/anodizing-interference-coloring
5 https://web.archive.org/web/20080908111117/http://www.anodizing.org/Anodizing/environment.html