Introduction
For the safety and effective distribution of power in industrial and commercial applications, Distribution boxes act as a critical component. These boxes comply with strict safety and regulatory standards, ensuring long-term reliability and safety even in the varying environments and operational conditions. Class 1 Div 1, NEMA 4X, RoHS, and UL508 are certifications that guarantee distribution boxes work safely and reliably. Certified distribution boxes reduce risks of fire, assure protection against water, ensure compliance to international safety and environmental standards, and ensure steady power distribution.
Class 1 Div 1 certification, in risky environments with flammable gases or vapours, ensures harmless operation. NEMA 4X Certification, shields against environmental aspects such as dust, water, and corrosion. RoHS Certification restricts hazardous materials by guaranteeing environmental sustainability. UL508 Certification creates safety standards for industrial control panels.
Class 1 Div 1 Certification
Reasons
Class 1, Division 1 (C1D1) certification is a safety standard which applies to the environment with recurrent explosion hazard such as flammable gases or liquids. C1D1 certification is a classification defined by NEC.
- C1D1 averts explosions and fires instigated by electrical equipment on sites where flammable gases, vapours, or liquids are present under normal operating conditions.
- Confirms the equipment operates safely in areas with continuous or recurrent contact to flammable materials.
- Oil and gas refineries, Petrochemical plants, Pharmaceutical manufacturing industries, and more require this certification for safety in hazardous environments.
Methods
Distribution boxes should be designed to prevent the explosion of surrounding flammable materials and contain cool in case of any explosion.
- Explosion-Proof Design made from heavy-duty materials like cast aluminum or stainless steel to contain internal explosions.
- Equipment enclosures must contain and prevent the ignition of hazardous gases.
- Use of non-sparking materials and corrosion-resistant components.
- Sealed channels, essentially safe circuits, and proper grounding to eliminate explosion causes.
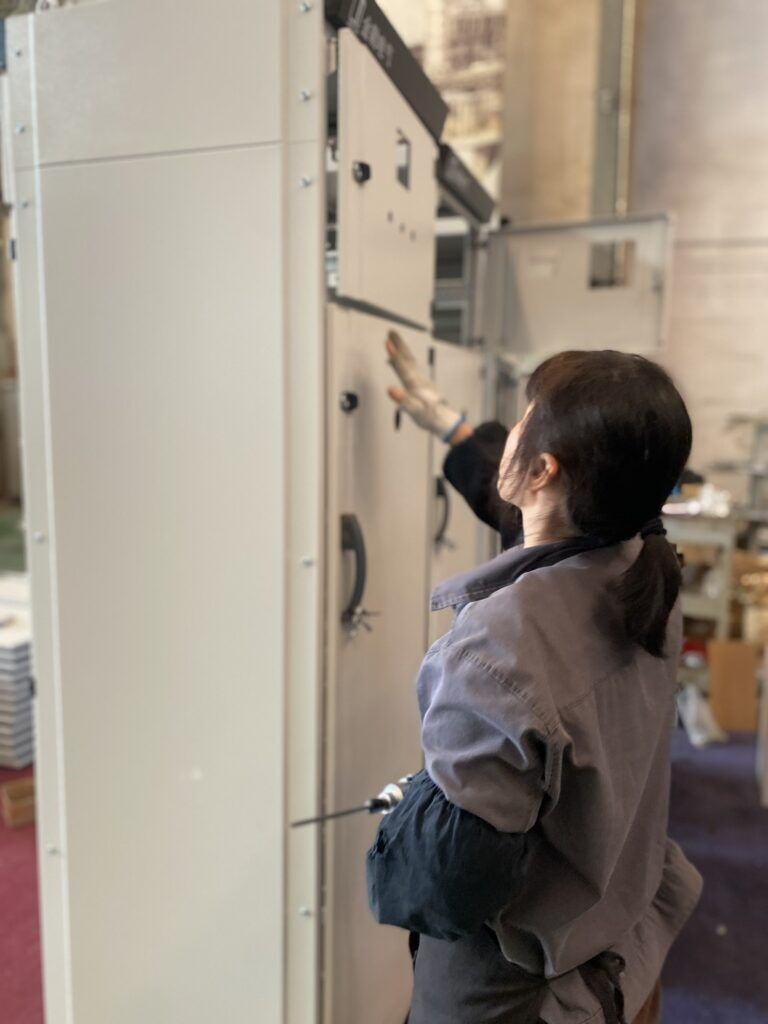
NEMA 4X Certification
Reasons
Industrial applications exposed to harsh environments such as outdoor and food processing facilities require NEMA 4X. NEMA 4X is a National Electrical Manufacturers Association (NEMA). It describes the level of protection against water, dust, and environmental hazards. NEMA 4X certification guarantees that distribution boxes can endure harsh environmental conditions, making them suitable for:
- Outdoor installations exposed to rain and dust.
- Areas where saltwater corrosion is a concern such as marine environments.
- Avoids entrance of airborne pollutants, such as dust, dirt, and debris.
Methods
To meet NEMA 4X waterproof and dustproof standards, enclosures should be designed with corrosion-resistant material such as powder-coated Aluminum, and sealed cable entry points for protection against contaminants:
- Neoprene and silicone to prevent dust and water ingress.
- Stainless steel or polycarbonate are corrosion-resistant materials which can withstand chemical exposure.
RoHS Certification:
Reasons
RoHS safeguards environmental and human health by restricting toxic materials in products. As it stands for Restriction of Hazardous Substances. RoHS stops dangerous chemicals from polluting landfills and water sources, using sustainable and recyclable components.
- Ensures human health by limiting revelation to toxic chemicals causing neurological disorders and cancer.
- Environmental Protection by diminishing hazardous waste, preventing air, soil, and water pollution.
Methods
Distribution boxes to achieve RoHS should be designed with tin-silver-copper solders, use non-toxic plasticizers, perform third-party testing using XRF:
- Implement strict quality control by performing material testing and certification.
- Monitor production processes by avoiding contamination with restricted substances.
- Use lead-free soldering techniques by ensuring that electronic assemblies do not contain harmful lead-based solders.
UL508 Certification
Reasons
UL 508 is a safety standard ensuring electrical safety, fire protection, and dependability for devices used in industrial automation, motor control, and process control applications. UL 508 applies to Industrial control panels, Relays and switches, Motor controllers, etc.
- Prevents electrical shocks, and short circuits in industrial environments.
- Verifies components endure high voltage loads, and extreme conditions, ensuring continuous operation without overheating or failure.
Methods
For UL508 compliance, distribution boxes must undergo the following Design and Testing, Component Selection, and Quality Control methods:
- Using UL-listed or UL-recognized parts to meet electrical safety standards.
- Surge and short-circuit protection mechanisms by enhancing the safety of electrical systems.
- Performing Electrical insulation tests byverifying dielectric strength and insulation resistance to prevent electrical failures.
- Ensuring heat dissipation, fire resistance, and durability.
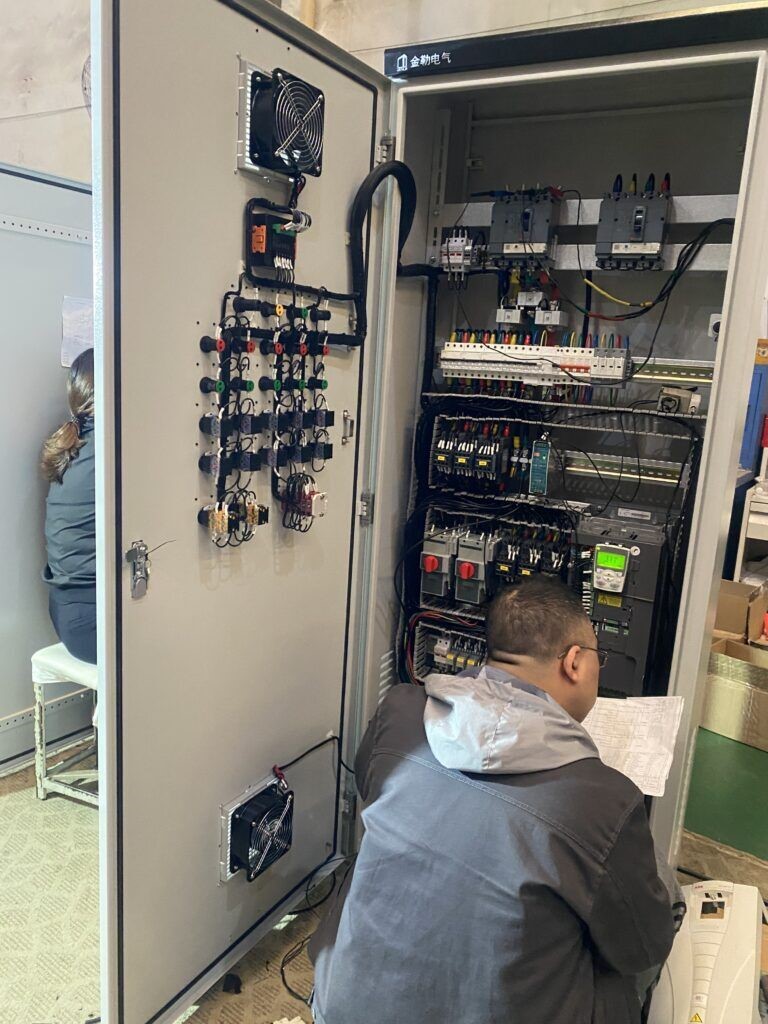
Technical and Process Approaches
Detailed Methods for Achieving Each Certification
The process of achieving compliance for each certification involves severe testing and engineering methodologies, from specialized wiring methods, such as sealed conduit systems for C1D1, to using stainless steel or reinforced plastic for NEMA 4x, X-ray fluorescence for RoHS, and using UL-listed components for UL-508 and many other methods discussed below are used for safety and reliability of distribution boxes to securely distribute power from one source to other circuits.
Class 1 Div 1: Implementing explosion-proof junction boxes and spark-preventive wiring techniques.
NEMA 4X: Using industrial-grade sealing gaskets and corrosion-resistant metals.
RoHS: Conducting X-ray fluorescence (XRF) analysis for material verification and ensuring lead-free soldering.
UL508: Performing high-voltage testing, electrical insulation verification, and continuity checks.
Specific Technologies and Processes Used
Encapsulation technology: Sealing electronic components in protective resins to prevent environmental exposure.
Gasketed enclosure design: Using IP-rated seals for superior ingress protection.
Thermal management systems: Ensuring well-regulated dissipation of heat to prevent overheating of electrical enclosures, protecting against moisture and mechanical damage
Automated compliance testing: Using AI-driven inspection techniques for high-accuracy verification.
Conclusion
Summary of Benefits of Compliance
Complying with Class 1 Div 1, NEMA 4X, RoHS, and UL508 standards ensures that distribution boxes are: Safe for use in hazardous locations, Resistant to environmental damage, Environmentally friendly and sustainable, Reliable and compliant with international regulations.
Future Outlook and Continuous Improvement
Manufacturers must continue improving their designs to meet evolving regulatory standards. Future advancements may include:
- Smart monitoring systems: Integrating IoT technology for real-time diagnostics and safety monitoring.
- Enhanced materials: Offering improved durability and corrosion resistance for extreme environments.
- Automation in testing: Using AI-driven inspections for precision compliance verification.
By adhering to these standards, manufacturers can ensure that their distribution boxes meet the highest safety, environmental, and performance requirements, providing reliable electrical solutions for diverse applications.
References
htttps://art-tangent.com/product/