Due to the growing demand for intricate and delicate components, the sheet metal industry has experienced a paradigm shift. The need for accurate and effective part manufacturing has increased across a range of industries including consumer goods, electronics, and aerospace and automotive. However, manufacturing components with complex forms and strict tolerances poses major hurdles.
Traditional sheet metal production technologies frequently fall short of meeting the complexity of modern designs. To solve this, a collaborative solution that combines smart software and specialized gear has emerged. By understanding the intricacies of complex geometries and the tools available to shape them, manufacturers can unlock new possibilities for product innovation and enhance their competitive edge.
The Challenges
The demand for intricate and complex geometries in components is causing a revolutionary shift in the sheet metal industry. The ongoing quest of innovation across a range of sectors is driving this trend. These companies are trying more and more to set themselves apart from the competition with unique and beautiful designs which often call for the incorporation of intricate geometries into sheet metal parts. Concurrently, there is an increasing focus on the utility of products leading to the creation of parts with intricate internal designs and characteristics that demand accuracy manufacturing.
Producing sheet metal components with such complex geometries in an efficient manner is a difficult task. While more straightforward shapes can be successfully manufactured using traditional sheet metal fabrication techniques, contemporary designs frequently demand greater precision and intricacy. When trying to produce components with precise tolerances, intricate details, and complex curves the limitations of traditional tooling and equipment become evident.
Furthermore, longer production times, higher costs, and inconsistent product quality can arise from these labor-intensive processes. To ensure the successful production of intricate sheet metal components, manufacturers are therefore forced to look for creative ways to get past these challenges.
Solutions
Advanced Software
The use of complex CAD/CAM software has become essential to handle the complexity of contemporary sheet metal designs. These software programs give engineers and designers the instruments they need to produce complex 3D models with unmatched accuracy and precision. Engineers can create complicated geometries that would be impossible to design with conventional techniques by utilizing sophisticated modeling capabilities. In addition, CAD/CAM software is essential for producing comprehensive manufacturing instructions that cover operations like bending cutting and forming. Through optimized toolpath generation and simulation, manufacturers can minimize material waste, reduce production time, and enhance overall efficiency.
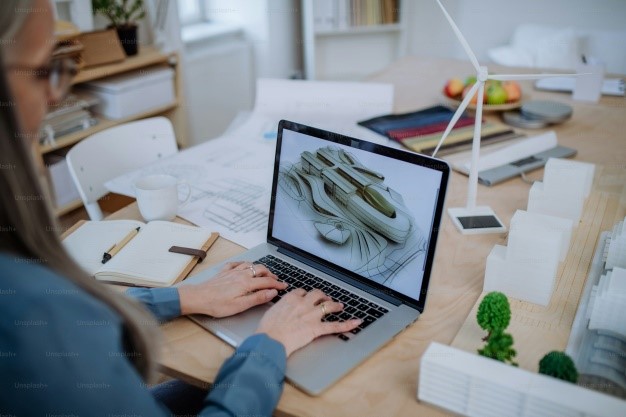
Precise Programming for Complex Geometries
The successful production of complex sheet metal components relies heavily on the ability to generate precise programming instructions. CAD/CAM software facilitates this process by providing a platform for creating detailed part programs that accurately define the required manufacturing operations.
Advanced programming techniques, such as adaptive compensation and toolpath optimization, are essential for achieving the desired component quality. Programmers can create dependable and effective part programs that reduce errors and rework by carefully taking into account variables like machine capabilities material properties and tool wear. Furthermore, manufacturing processes can be virtually tested with simulation software which makes it possible to find and fix any problems before actual production starts.
Specialized Machinery
Customized equipment that can handle complex shapes and tight tolerances must be used in the fabrication of complex sheet metal components. When processing sheet metal multi-axis machines—which have several axes of motion—offer unmatched flexibility and accuracy. These devices have remarkable accuracy and repeatability in a variety of tasks such as bending forming and cutting. With multi-axis machines manufacturers can create components with intricate surfaces curves and features that would be difficult or impossible to accomplish with conventional machinery.
In the process of producing intricate sheet metal assemblies robotic welding systems—along with multi-axis machines—have gained significance. These systems provide welding operations with high degrees of consistency accuracy and speed. Manufacturers can save labor expenses generate more efficient products and increase productivity by automating the welding process. Robotic welding systems also make it possible to create intricately geometrized weldments like those found in aerospace and automotive components.
Benefits
In terms of productivity, accuracy, and capacity, the combination of cutting-edge software and specialty equipment in sheet metal fabrication produces noteworthy advantages. Manufacturers can cut costs and lead times by optimizing the design and manufacturing processes with the use of advanced CAD/CAM software. Optimizing and simulating manufacturing processes before actual production reduces mistakes waste and rework which boosts productivity and makes better use of available resources. Further boosting productivity and cutting labor costs is the automation of different production stages via robotic systems.
The combination of advanced software and specialized machinery also leads to enhanced precision and accuracy in component production. Precise manufacturing instructions are based on highly accurate and detailed digital models created with the aid of CAD/CAM software. Robotic systems and multi-axis machines provide outstanding repeatability and accuracy guaranteeing that parts meet strict requirements and tolerances. In sectors where component performance and reliability are crucial like aerospace and automotive, this level of precision is essential. A manufacturer’s ability to work with complex designs is increased by adopting these technologies.
Efficient and economical production is now possible for complex geometries that were previously deemed impractical or unnecessarily expensive. The precision of robotic welding systems and the adaptability of multi-axis machines allow for the creation of components with intricate features and assemblies. This increased capacity enables producers to provide a greater range of goods and services while also satisfying the changing needs of the market.
Conclusion
The proficient handling of complex geometries in sheet metal components necessitates a strategic approach employing advanced software and customized machinery. Manufacturers are able to efficiently design and program complex items with the use of CAD/CAM software. Precision and flexibility required for manufacturing are provided by robotic welding systems and multi-axis machines. When combined, these technologies assist companies in handling more complex designs, improving product quality, and boosting productivity. As technology advances, it is expected that new channels for manufacturing intricate sheet metal components will open up stimulating innovation in a range of industries. A tactical strategy utilizing specialized tools and cutting-edge software is required to handle complex geometries in sheet metal components efficiently. Manufacturers are capable of designing and programming complex products with efficiency when they use CAD/CAM software.
External links:
https://en.wikipedia.org/wiki/Sheet_metal
https://cdn2.hubspot.net/hubfs/340051/Design_Guides/Xometry_DesignGuide_SheetMetal.pdf